Wednesday, 21 June 2023, Bengaluru, India
Volkswagen’s battery company PowerCo SE claims to have created a ground-breaking technique that will considerably improve sustainability and efficiency in the production of large quantities of battery cells. The corporation intends to implement a brand-new manufacturing method employing a dry coating technology in its facilities in Northern America and Europe.
PowerCo will work with the German company Koenig & Bauer AG to advance and industrialize the dry coating process, which the company believes can reduce production costs by millions of euros, as well as energy consumption by roughly 30% and floor space requirements by 15%.
Thomas Schmall, Chairman of the Supervisory Board of PowerCo SE and Group Board Member for Technology at Volkswagen AG, commented on the development, “The technological prowess of PowerCo is demonstrated through innovations like dry coating. We have the requisite skills and qualified personnel to advance cell production and provide considerable cost advantages to our clients. Our goal is to start industrial battery production that is both economical and sustainable.“
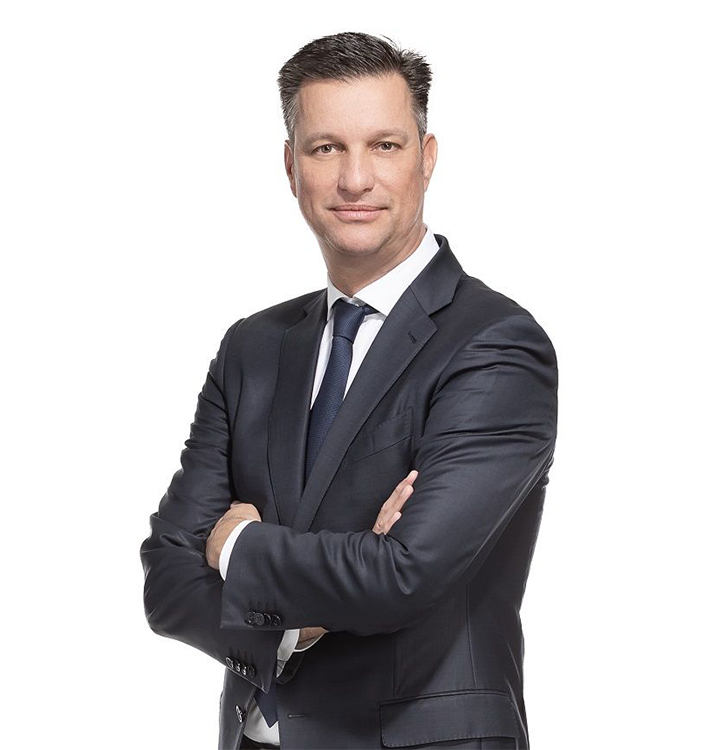
PowerCo and Koenig & Bauer have a joint development agreement in place to accomplish this objective. The businesses will work together to create a roller press for powder coating electrodes on an industrial scale. The dry coating process enables the production of electrodes without wet coating and drying them afterward at high prices.
The most energy-consuming step in cell manufacturing, as well as the use of chemical solvents, are no longer necessary with the new method. The technology is already being tested and improved by PowerCo in a trial line at one of its labs in Northern Germany. Koenig & Bauer, a printing expert, will create a machine for commercial powder coating, according to the business.
Dry Coating is a true game changer for production, similar to what the solid-state cell is for the end product. If successfully scaled, it will provide us with a distinct position on the market and unquestionable competitive advantages, according to PowerCo SE CEO Frank Blome.
The electrodes, which include the cathode and anode, are what define energy density and battery performance in a battery cell. In the manufacturing of industrial electrodes today, additives and liquid solvents are combined with the battery ingredients to create a slurry. They are then covered with copper or aluminium foils, dried, and calendered.
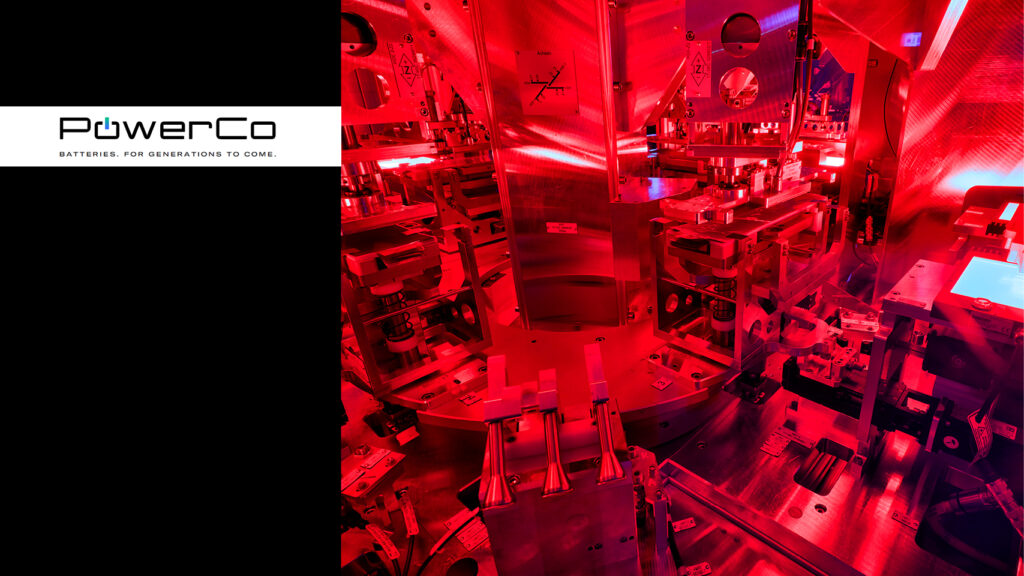
With the help of PowerCo’s dry coating process, it is possible to print-like directly onto the foil of the powdery fundamental components. As a result, two of the four process stages used to make electrodes are no longer necessary.
Applying the powder coating on the foil in an incredibly precise and even manner results in a layer that is roughly the thickness of a hair. According to PowerCo, this ensures a high spatial energy density, a long life cycle, and an improved battery’s capacity to charge quickly.
[Source of Information: etn. news]